Agentes desmoldeantes
Líderes globales en el desarrollo de innovadores agentes desmoldeantes
Los agentes desmoldeantes son parte integral de muchos procesos de fabricación. Los agentes desmoldeantes especiales pueden ayudarle a mejorar la productividad, aumentar la vida útil de útiles, moldes de fundición y de inyección, aumentar los tiempos de ciclo, mejorar la calidad de piezas y superficies y reducir las tasas de rechazos y defectos, entre otras muchas potenciales ventajas.
Colaboramos estrechamente con usted y con su equipo para encontrar los agentes desmoldeantes adecuados que contribuyan a mejorar sus procesos.
Agentes desmoldeantes convencionales
Ofrecemos una amplia gama de agentes desmoldeantes convencionales (para añadir en cada ciclo) según las necesidades de nuestros clientes. Nuestros agentes desmoldeantes convencionales aportan las siguientes ventajas:
- Disponibles con base agua o con base disolvente
- Formulados para uso directo o diluido, según la aplicación
- Adecuados para muchos tipos de equipos de pulverización
- Con diferentes tasas de dilución a medida, según la aplicación y características de fluidez deseadas
- Altamente adecuados para piezas moldeadas con geometría complicada
- Extraordinaria reducción de la cantidad de residuos e incrustaciones en los moldes
Agentes desmoldeantes semipermanentes
Las sofisticadas tecnologías actuales de agentes desmoldeantes semipermanentes con base agua o disolvente le ofrecen gran cantidad de potenciales ventajas. La tecnología de desmoldeo semipermanente ha aportado a la industria una alternativa viable a los agentes desmoldeantes tradicionales que se aplican de forma generalizada en formato aerosol o que se añaden en cada ciclo consumiendo grandes volúmenes. Ventajas para nuestros clientes:
- Más desmoldeos entre aplicaciones que con soluciones de desmoldeo convencionales
- Más ciclos de moldeado por turno de trabajo
- Solo una pequeña cantidad de producto por aplicación, para un entorno de trabajo más limpio y menores necesidades de almacenamiento
- Reducción de tasas de rechazo
- Vida útil de los moldes mucho más larga, gracias a sus cualidades protectoras
- Fabricación de diseños complicados de piezas y moldes, gracias a la sencilla y más precisa aplicación del agente desmoldeante
- Buena apariencia superficial de sus piezas moldeadas
Agentes desmoldeantes sin silicona
Chem-Trend ha desarrollado una gama extraordinariamente potente de agentes desmoldeantes sin silicona innovadores y sostenibles. Los agentes desmoldeantes sin silicona ofrecen una larga serie de ventajas:
- Reducen el residuo aceitoso, permitiendo así un pintado y revestimiento más fáciles tras el desmoldeo
- Reducen el riesgo de contaminación y eliminan costosos pasos del proceso de fabricación, con lo que contribuyen a aumentar la productividad y reducir los costes de producción
¿Por qué decidirse por los agentes desmoldeantes de Chem-Trend?
Valor verdadero
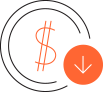
Nuestro objetivo es crear valor para usted, nuestro cliente. Formulada para optimizar sus operaciones diarias, nuestra línea líder en el sector de agentes desmoldeantes incluye productos con base agua y con base disolvente, así como productos con y sin silicona en productos semipermanentes o convencionales. Con nuestras soluciones puede superar los costosos problemas de fabricación y aprovechar además la eficacia de los agentes desmoldeantes para mejorar la eficiencia operativa y la calidad del producto.
Productividad llevada al máximo
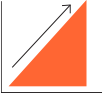
Chem-Trend ofrece una amplia variedad de opciones de agentes desmoldeantes diseñados para responder a sus necesidades específicas y maximizar sus resultados. Cada proceso de moldeado es único de alguna forma y exige soluciones específicas para un desmoldeo óptimo. Nuestro equipo de expertos in situ adopta un enfoque práctico, colaborando con usted para identificar todas las áreas de mejora potencial. Y nuestro equipo de I+D diseña soluciones a medida para sus operaciones.
Sostenibilidad probada
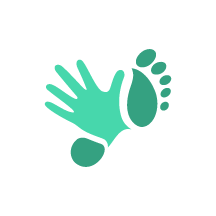
Muchos de nuestros clientes trabajan sin descanso para conseguir que sus operaciones sean más sostenibles. Eligen Chem-Trend porque desde nuestros comienzos nos hemos centrado en minimizar el impacto ambiental de nuestros productos.En los años sesenta desarrollamos y lanzamos al mercado el primer agente desmoldeante con base agua, el cual tuvo un efecto muy positivo en la seguridad y salud de las instalaciones de moldeo por fundición a presión al prescindir del uso de grafito y disolventes en los agentes desmoldeantes, tan utilizados entonces.Los continuos esfuerzos se extendieron a otros aspectos ambientales, como el uso de compuestos orgánicos volátiles (COV) en los agentes desmoldeantes con base disolvente. Actualmente, Chem-Trend es líder en el desarrollo de soluciones innovadoras.
NOVEDADES
PENSAMIENTO RELACIONADO
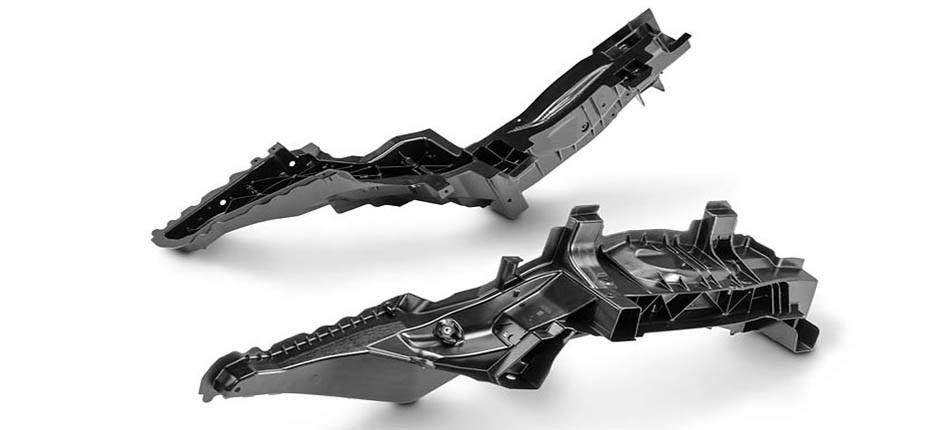
El desmoldeante adecuado para una mayor eficiencia y sostenibilidad
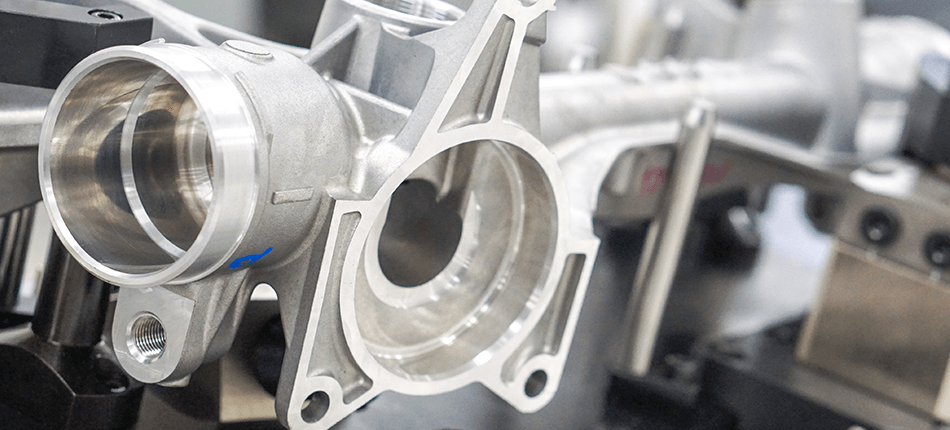
Efecto de los agentes desmoldeantes para moldeo por fundición a presión sobre el equilibrio térmico de los moldes
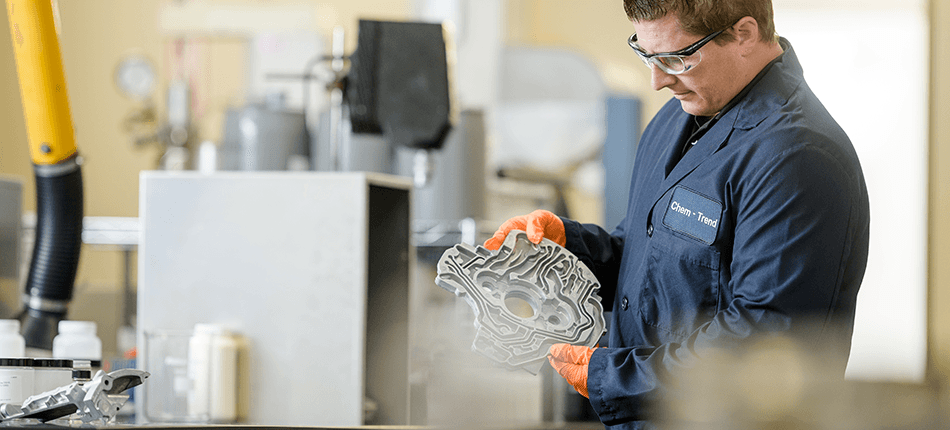
Tecnologías innovadoras en agentes desmoldeantes

Tendencias innovadoras en lubricantes para troqueles para mejorar la productividad y los requisitos del proceso
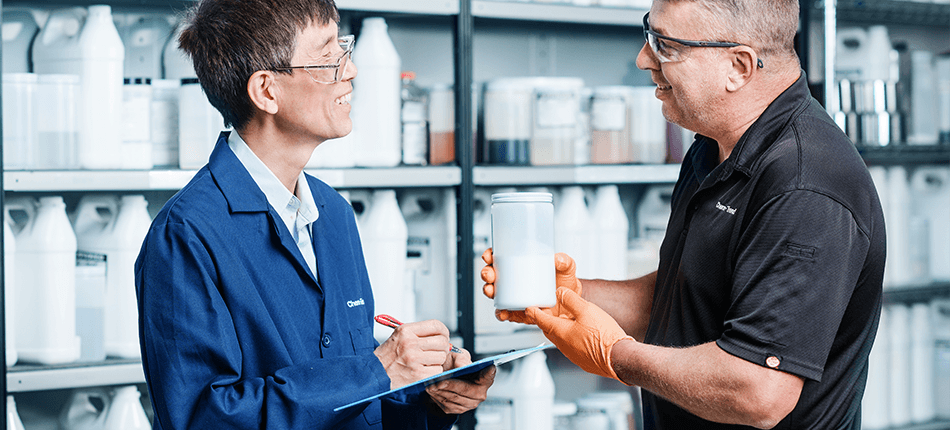
Tecnología y tendencias de los agentes desmoldeantes y lubricantes para el moldeo de aluminio por fundición a presión
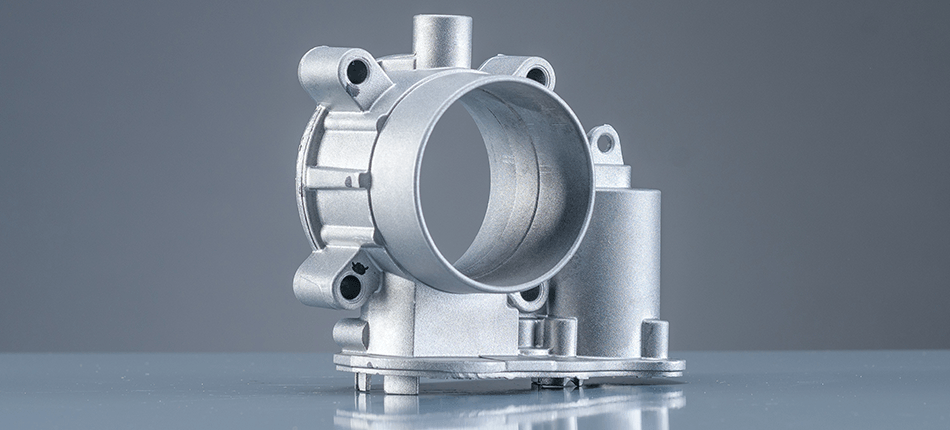
Tecnología y tendencias de los agentes desmoldeantes y lubricantes para el moldeo de magnesio por fundición a presión
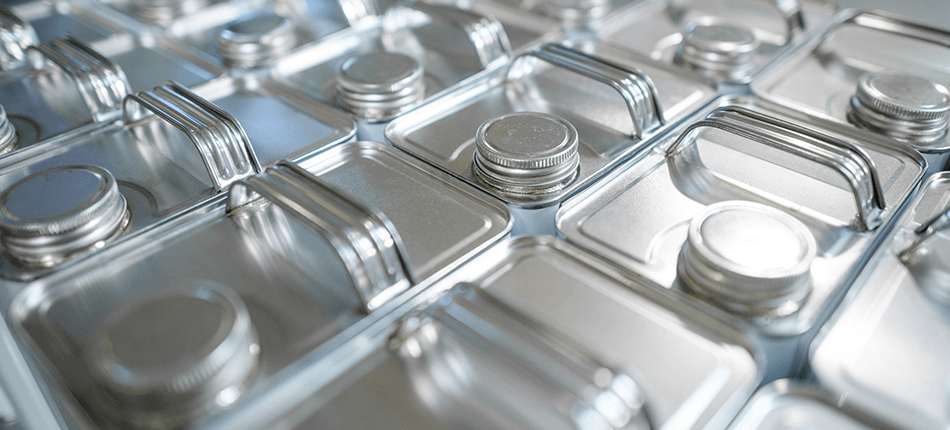
Agentes desmoldeantes: La adherencia de los recubrimientos y el uso de productos auxiliares antiestáticos
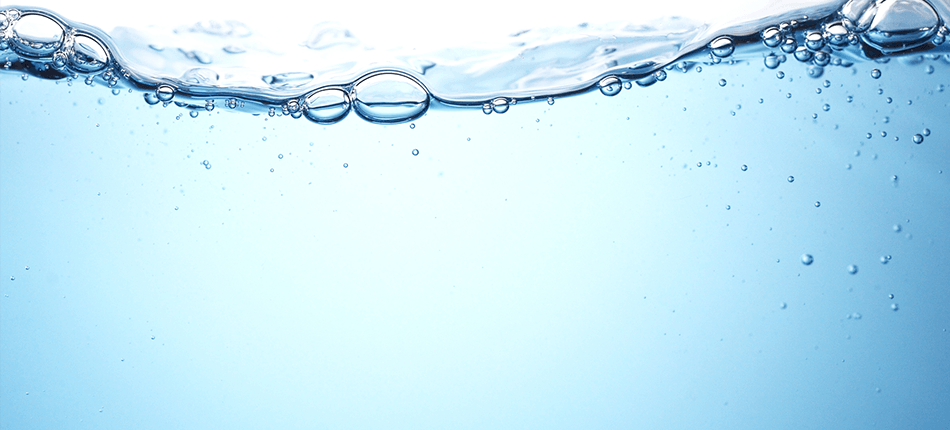
Ahorro de agua mediante la utilización de lubricantes de altas prestaciones para troqueles
FOLLETOS
HERA™ Agentes desmoldeantes para moldeadores
HERA™ tiene usos muy versátiles: para aleaciones estándar y también para aleaciones especiales altamente dúctiles, para piezas con geometrías complejas y para un amplio rango de temperaturas de molde.
Los agentes desmoldeantes HERA™-Light son aptos para todos los procesos de aplicación en el moldeo por fundición a presión
El agente desmoldeante HERA™-Light se caracteriza por la buena adherencia de la capa desmoldeante en un amplio rango de temperaturas del molde y la capa se forma muy rápidamente.
Obtenga más información en nuestro folleto.
Los desmoldeantes Chem-Trend® SL-6XXXX para fundidores contribuyen a la satisfacción de las necesidades de la industria del procesamiento de materiales
Las piezas producidas por inyección a presión con desmoldeantes Chem-Trend® SL-6XXXX admiten tratamientos de cataforesis o KTL y pueden unirse mediante soldadura.
Obtenga más información en nuestro folleto.
Catálogo de Productos de Mantenimiento de Moldes y Agentes Desmoldeantes Lusin®
Solución completa para una mayor eficiencia
Proteja sus extensas inversiones en moldes de inyección y maquinaria. Los productos de mantenimiento de moldes y los agentes desmoldeantes Lusin® ofrecen un rendimiento óptimo y una mayor productividad en diferentes procesos de producción: moldeo por inyección, moldeo por soplado, extrusión y composición.
PREGUNTAS FRECUENTES
El cambio depende en gran medida de la industria y de los requisitos del proceso. Algunas industrias ya no toleran los productos con base disolvente debido a problemas de salud, seguridad y medio ambiente o a otras cuestiones normativas. Industrias como la fundición a presión, la fabricación de neumáticos y el moldeo de caucho en general utilizan predominantemente agentes desmoldeantes con base agua. La industria del poliuretano utiliza agentes desmoldeantes tanto de base agua como de base disolvente, mientras que las industrias de composites y termoplásticos utilizan principalmente agentes desmoldeantes de base disolvente.
Los productos de base agua son más sensibles a la aplicación (ofrecen más problemas para la formación de capa) y tienen velocidades de evaporación más lentas (que pueden verse influidas por el método de aplicación, las condiciones del proceso y los niveles de humedad del entorno) que los productos de base disolvente.
Los productos de base agua son más propensos a provocar la interacción química del agua residual que queda en la superficie del molde con el material que se moldea durante el proceso de moldeo (p. ej., la generación de urea por los productos en el moldeo de poliuretano).
Esta categoría de agentes desmoldeantes también requiere más tecnología para garantizar la estabilidad de la emulsión y la resistencia a la bioactividad. Hay que hacer frente a estos retos para extender el uso de agentes desmoldeantes de base agua a una variedad más amplia de industrias.
Los productos sin aerosol se aplican mejor utilizando una pistola de pulverización de alta calidad o con un equipo de pulverización controlado por tiempo.
Los productos sin aerosol se aplican mejor en el procesado de termoplásticos utilizando una pistola de pulverización de alta calidad o con un equipo de pulverización controlado por tiempo.
La metodología de aplicación depende del soporte elegido, así como de la naturaleza del agente desmoldeante y del proceso y su entorno. La aplicación es un aspecto clave que debe tenerse en cuenta y que puede influir significativamente en el rendimiento del agente desmoldeante. En la mayoría de los casos, los agentes desmoldeantes se aplican mediante una pistola pulverizadora (aplicación manual o robotizada). En algunas aplicaciones se utilizan sistemas de pulverización programables con múltiples boquillas de pulverización que permiten la aplicación de uno o más agentes desmoldeantes. El tamaño de la boquilla se regula para garantizar una atomización adecuada (influida por el rendimiento previsto y la viscosidad del agente desmoldeante) y una buena formación de la película. La aplicación por pulverización puede ser asistida por aire (donde se utiliza aire para fragmentar y atomizar aún más las gotitas) o sin aire (donde la boquilla a alta presión fragmenta el chorro de agente desmoldeante para obtener la atomización necesaria). Las pistolas electrostáticas también pueden utilizarse para aplicar agentes desmoldeantes sólidos y líquidos. En algunas aplicaciones, los agentes desmoldeantes también pueden aplicarse mediante aerosoles o incluso limpiando de forma manual o automatizada.
Cada tipo de agente tiene sus propias ventajas (V) e inconvenientes (I). Le ofrecemos aquí un resumen según tipo de agente desmoldeante:
Agentes desmoldeantes de base disolvente:
V: Más fáciles de aplicar. El soporte del disolvente también contribuye a la formación de la película. La velocidad de evaporación puede ajustarse en función de la mezcla de disolventes. La elección del disolvente puede facilitar la disolución / dispersión de los ingredientes activos del agente desmoldeante.
I: No son respetuosos con el medio ambiente. Provocan mayores problemas para la salud (COV) y de seguridad (riesgo de incendio) que los productos sin disolventes.
Agentes desmoldeantes de base agua:
V: Respetuosos con el medio ambiente y no suponen riesgo de incendio. A veces pueden ser diluibles (pueden suministrarse como concentrados). Pueden utilizarse para enfriar el molde si es necesario. Pueden desarrollarse con un nivel de tecnología que garantice un rendimiento del agente desmoldeante equivalente al de los agentes desmoldeantes con base disolvente.
I: Requieren una tecnología más compleja para su fabricación. La formación de una capa adecuada puede ser más difícil. Esta categoría de agentes desmoldeantes puede ser más propensa a problemas de estabilidad y ataques biológicos. Los agentes desmoldeantes de base agua tienen velocidades de evaporación más lentas que los de base disolvente y pueden no ser apropiados para algunas operaciones de moldeo a temperatura ambiente u operaciones con tiempos de ciclo cortos. El agua residual en el molde puede afectar al rendimiento del moldeo (vapor atrapado) o incluso reaccionar químicamente con el material que se está moldeando. Esto último es especialmente problemático en el moldeo de piezas de poliuretano.
Agentes desmoldeantes sin soporte:
V: Pueden aplicarse «tal cual» debido a la ausencia de soporte. No hay emisión de vapores. Se observa una aplicación menos ruidosa. No requiere dilución ni almacenamiento en depósito. No hay ningún caudal de residuos.
I: Pueden crear peligro por polvo si no se aplican correctamente. Requieren un equipo de aplicación especial (a menudo, pistolas de pulverización electrostática), que puede requerir una inversión costosa. El uso de agentes desmoldeantes sin soporte también puede requerir modificaciones adicionales en el equipo de moldeo para garantizar el equilibrio térmico del molde. Estos factores limitan a menudo la aplicación de esta categoría de agentes desmoldeantes.
Agentes desmoldeantes de sacrificio:
V: Fáciles de aplicar. Precisan menos técnica para su aplicación y ofrecen más tolerancia de trabajo (dependen menos de operarios formados).
I: Tienden a la formación de acúmulos en el molde si se aplican en exceso. En general, la capa de desmoldeante se transfiere parcialmente a la pieza moldeada, lo que puede provocar efectos secundarios negativos en las operaciones posteriores al moldeo (pintura, adhesivado, etc.) si se aplica en exceso o si la química del agente desmoldeante no es compatible con la operación posterior al moldeo. Si son de base agua, tienden a enfriar el molde, quitando calor y energía al sistema (esto puede representar un inconveniente si el proceso no está diseñado para ello).
Agentes desmoldeantes semipermanentes:
V: Requieren una frecuencia de aplicación significativamente menor que los agentes desmoldeantes de sacrificio porque la capa de agente desmoldeante dura varios ciclos de moldeo (la frecuencia depende de las condiciones del proceso). Permiten una producción más constante y continuada sin interrupciones para aplicar agente desmoldeante. Hay muy poca transferencia a la pieza moldeada, lo que permite mejores operaciones posteriores al moldeo (recubrimiento, adhesivado). El agente desmoldeante puede reaplicarse regularmente sobre el molde recubierto refrescando la película de agente desmoldeante. Esta categoría de agentes desmoldeantes proporciona una excelente combinación de barreras químicas y físicas, evitando la formación de acumúmulos y proporcionando el rendimiento de desmoldeo deseado.
I: Requiere más formación de los operarios para garantizar que se respeta la frecuencia de retoque correcta. Los moldes deben estar limpios para permitir una buena interacción entre el agente desmoldeante y la superficie del molde durante la aplicación inicial del desmoldeante.
Agentes desmoldeantes internos:
V: Reducen la necesidad de agentes desmoldeantes externos.
I: Pueden seguir exudando a la superficie con el tiempo, comprometiendo las operaciones posteriores al moldeo (recubrimiento y adhesivado) o la estética de la superficie de la pieza. A menudo no evitan la necesidad de utilizar agentes desmoldeantes externos, ya que los desmoldeantes internos no siempre migran a la interfaz del molde o quizás no garanticen una eficacia de desmoldeo del 100 %. Tienen una capacidad limitada para desempeñar funciones como agente desmoldeante de alto rendimiento, ya que, por ejemplo, afectan a las características superficiales de la pieza.
La ventaja de los agentes desmoldeantes que contienen silicona es que ofrecen un efecto de desmoldeo muy bueno. La desventaja de los agentes desmoldeantes que contienen silicona es que el tratamiento posterior de las piezas desmoldeadas, como el adhesivado o la pintura, puede resultar difícil o incluso imposible. Será necesario un tratamiento posterior adicional de la pieza.
Los agentes desmoldeantes no sólo proporcionan una barrera física y/ o química como medio de separación entre el material que se moldea y la superficie del molde, sino que también influyen en las características del proceso, como la velocidad de flujo del material que se moldea dentro de la cavidad del molde, la duración del ciclo de moldeo y, por supuesto, la facilidad de desmoldeo. La elección de los agentes desmoldeantes también afecta a las características de acabado de la pieza desmoldeada, como el nivel de brillo, la reproducción precisa de la textura, las operaciones posteriores al moldeo (como el adhesivado o el recubrimiento de la pieza moldeada), además de influir en la vida útil del molde entre ciclos de mantenimiento y en la productividad general.
Entre los factores que deben tenerse en cuenta para seleccionar el agente desmoldeante adecuado se incluyen:
- Material del molde / sustrato
- Material que se va a moldear
- Condiciones del proceso:
– Temperatura
– Velocidad de la línea / tiempo de ciclo
– Presión
– Proceso de moldeo específico, como moldeo por inyección, alta presión, llenado por gravedad, compresión, etc.
– Fluctuaciones de las variables del proceso - Geometría del molde
- Operaciones posteriores al moldeo (adhesivado, recubrimiento)
- Nivel de rendimiento y productividad esperados (número de desmoldeos correctos o de piezas correctas desmoldeadas por período de tiempo)
- Problemas existentes en el proceso (de llenado de cavidades, soldadura, tasas de desechos en relación con el desmoldeo, fluctuaciones de las condiciones del proceso, etc.)
- Expectativas de mantenimiento del molde (frecuencia de limpieza del molde)
- Requisitos de acabado de las piezas (brillo, daños, etc.)
- Metodología de aplicación
- Requisitos de Prevención de Riesgos Laborales (PRL)
Aplicar demasiado agente desmoldeante puede dificultar el tratamiento posterior de las piezas, al crear una superficie aceitosa o resbaladiza en la pieza moldeada.
La ventaja de los botes de aerosol para el procesado de termoplásticos es que el sistema de válvula de pulverización permite aplicar el producto de forma muy fina, uniforme y con un patrón de pulverización predecible. Esto permite ahorrar material y evita la aplicación excesiva. Los botes de aerosol también ofrecen un fácil manejo y flexibilidad.
La acumulación de agentes desmoldeantes, del material que se está moldeando o de los subproductos y residuos generados por las reacciones químicas que tienen lugar dentro de la cavidad del molde (en situaciones en las que el compuesto cambia químicamente a lo largo del proceso de moldeo) afecta negativamente al rendimiento del moldeo en términos de transferencia de calor, propiedades dimensionales de la pieza, aspecto y eficiencia del proceso.
Debe limpiarse periódicamente la suciedad de la cavidad del molde por medios mecánicos o químicos para garantizar la calidad de la pieza. Cada vez que hay que limpiar el molde en las instalaciones o realizar cualquier otro tipo de mantenimiento, se pierde productividad.
Los problemas de formación de acúmulos pueden tener dos causas principales:
Exceso de agente desmoldeante en el molde.
Esto puede deberse a una mala elección del agente desmoldeante para la aplicación específica (p. ej., que no sea compatible con la temperatura del proceso) o a una aplicación excesiva de agente desmoldeante en el molde.
La falta de barrera de desmoldeo provoca la formación de acúmulos del material que se está moldeando o de subproductos y residuos generados durante el proceso de moldeo.
En este caso, puede ser que la elección del agente desmoldeante no sea la adecuada para las condiciones del proceso (no adecuado para la temperatura del proceso, formación deficiente de la película, etc.). También puede ser que la aplicación sea deficiente (que no haya suficiente capa de agente desmoldeante en el molde) o que la resistencia física y/ o química del desmoldeante al material no sea suficiente, que penetre en la película de desmoldeante y se adhiera física o químicamente al molde.
Las industrias están moldeando materiales cada vez más innovadores para producir piezas con mejores prestaciones en condiciones cada vez más exigentes en las que funcionan los productos acabados. Estos materiales innovadores no siempre son fáciles de moldear. Un buen ejemplo está en el sector de la automoción, donde los componentes de los motores (piezas moldeadas) están sometidos a desafíos químicos y físicos para resistir condiciones operativas más agresivas. Como resultado, se necesitan materiales de nuevo desarrollo más resistentes para moldearlos a altos índices de producción con niveles mínimos de desechos. Esto supone un reto para la industria de los agentes desmoldeantes, debido a sus propiedades químicas y físicas, que dificultan su moldeo y desmoldeo.
El aspecto de las piezas también es ahora más exigente y, en muchos casos, las piezas se utilizan según salen moldeadas, con un acabado posterior mínimo. El sector de la automoción exige que los componentes de alta visibilidad, como volantes o salpicaderos, tengan propiedades estéticas muy elevadas (p. ej., textura, brillo y resistencia a daños) directamente después del desmoldeo.
En los últimos años, el moldeo a alta preisón de aluminio ha experimentado un aumento de la complejidad de los moldes, con un incremento del moldeo de alta integridad (semisólido y por compresión), así como una reducción de los tiempos de ciclo y un mayor aumento de las temperaturas de los troqueles.
Estos factores precisan que el agente desmoldeante ofrezca mejores propiedades antisoldadura, así como mejores propiedades de desmoldeo y lubricación para producir piezas de calidad en las condiciones de moldeo más difíciles. Esto debe lograrse sin comprometer otros atributos de rendimiento del agente desmoldeante.
También se crean diseños de moldes más complejos y sofisticados para otros sectores industriales, como los neumáticos de perfil bajo que fabrican los fabricantes de neumáticos. Estos diseños de moldes exigen un mayor rendimiento a los agentes desmoldeantes en lo que respecta a la facilidad de desmoldeo y la fluidez del caucho. El aspecto de los neumáticos una vez moldeados también es de vital importancia, lo que plantea retos significativos a la hora de desmoldear fácilmente y, al mismo tiempo, alcanzar unos estándares estéticos elevados.
El uso de productos con menos COV (compuestos orgánicos volátiles) sigue cobrando fuerza en las instalaciones productivas como consecuencia de la normativa de PRL, siendo especialmente importante en los procesos que requieren una mayor implicación directa de los operarios, como en el sector de los composites. Se seguirá prestando más atención al desarrollo de productos más respetuosos con el medio ambiente y de un uso más seguro. Esto estimulará el desarrollo de nuevos agentes desmoldeantes que sean capaces de cubrir estas necesidades sin dejar de ofrecer el mismo o mayor nivel de prestaciones que los productos actualmente en uso.
La mejor forma de aplicar los agentes desmoldeantes a granel es mediante una pistola pulverizadora o un pulverizador de ciclo controlado.